Processo di pulizia e reinstallazione semplificato
Alimentare - Tempi di fermo significativamente ridotti per un mulino attivo 24 ore su 24
Bob’s Red Mill Natural Foods Inc., USA, macina una vasta gamma di farine, cereali e semole 24 ore al giorno, 6 giorni a settimana.
L’azienda affrontava una sfida significativa legata ai tempi di inattività, causata dalla complessità delle operazioni di pulizia e reinstallazione dei tradizionali connettori a morsetto e manicotto durante i frequenti cambi di produzione.
Inoltre, era fondamentale trovare una soluzione per eliminare le perdite di polvere dai connettori all'interno dello stabilimento, garantendo un ambiente di lavoro più sicuro e pulito.
Dall'installazione dei BFM® fitting sulla linea di produzione, l'azienda è riuscita a ridurre drasticamente i tempi di fermo e a ottimizzare sia l'efficienza produttiva che l'igiene degli ambienti di lavoro.
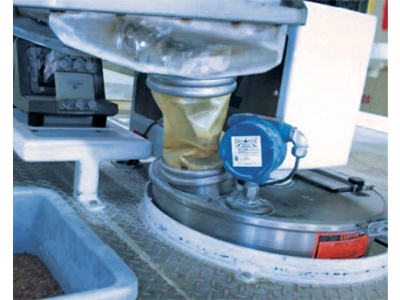
La Sfida BFM®
Ogni macchina è progettata per confezionare una varietà di prodotti, il che richiede una pulizia accurata e frequente tra un lotto e l'altro.
Le connessioni tra lo scarico del vaglio vibrante e l’ingresso dell’alimentatore a coclea erano difficili da raggiungere, e i tradizionali connettori a morsetto e manicotto richiedevano tempi prolungati per essere rimossi, puliti e reinstallati durante i cambi di produzione.
Questo non solo causava tempi di fermo significativi e rischi per la sicurezza degli operatori, ma, se installati in modo scorretto, i connettori potevano staccarsi, provocando perdite di prodotto e imprecisioni nel dosaggio.
Anche quando montati correttamente, i connettori tradizionali tendevano comunque a perdere prodotto, rendendo necessaria una pulizia costante per garantire l'igiene.
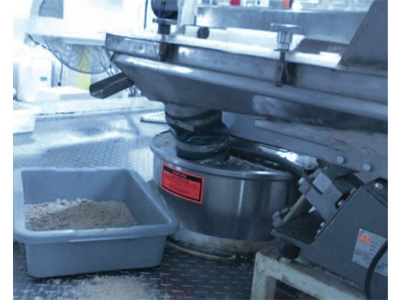
La Soluzione BFM®
Dopo aver scoperto il BFM® fitting durante una fiera, l'azienda ha installato due connettori Seeflex 040E sugli scarichi del vaglio e sugli ingressi dell’alimentatore a coclea per testarli.
Fin da subito è stata riscontrata una notevole riduzione del tempo necessario per rimuovere, pulire e sostituire i connettori. La lunghezza predefinita e il sistema di installazione senza attrezzi hanno reso il montaggio semplice e rapido ad ogni intervento.
Il design ermetico sigilla completamente il prodotto all’interno del sistema di produzione, eliminando le perdite di polvere e azzerando il rischio di contaminazione incrociata. L'efficienza del confezionamento e l'igiene generale dello stabilimento sono migliorate drasticamente. Di conseguenza, tutti i connettori dello stabilimento sono stati sostituiti con i BFM®.
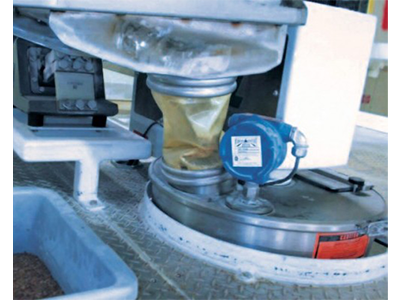
Benefici Ottenuti:
Cambi rapidi
Il sistema snap-fit del BFM® fitting semplifica i cambi rendendoli facili e veloci, mentre la lunghezza standard assicura sempre un'installazione precisa, eliminando i problemi di accuratezza nel dosaggio.
Migliore Igiene
Nessuna perdita di polvere, con l'eliminazione del rischio di contaminazione incrociata tra i prodotti e una significativa riduzione dei costi di pulizia.
Riduzione dei tempi di fermo
La pulizia rapida ed efficiente tra un lotto e l’altro ha ridotto drasticamente i tempi di inattività, ottimizzando la continuità produttiva.
Salute e sicurezza
L'assenza di attrezzi necessari per rimuovere o installare il connettore in posizioni difficili rende le operazioni molto più sicure per il personale.
Superintendent of Engineering and Maintenance
"Sono una delle migliori soluzioni che abbiamo mai trovato... Dopo aver installato i primi due connettori, abbiamo iniziato a sostituire tutti i connettori a morsetto e manicotto rimanenti nello stabilimento con i BFM® fittings. Li sto installando ovunque ci sia un punto di trasferimento, perché rendono il lavoro degli operatori molto più semplice."
Case study fornito per gentile concessione del distributore BFM® Powder-Solutions Group (Stati Uniti).